Mobile robotics replaces the term "driverless transport" and includes various autonomous vehicles that differ in their application and equipment. But what are the characteristics of the individual vehicles in detail and how does the ARCOS vehicle software facilitate the decision of plant operators to differentiate between the individual autonomous vehicles?
Share article
Mobile robotics has experienced a significant upswing in recent years and is increasingly used as the overall term for autonomous vehicles and means of transportation. In the past, people often spoke of "driverless transportation" to refer to autonomous, self-driving transportation vehicles. Today, however, the term "mobile robots" has become widely established, roughly combining three different autonomous vehicles while reflecting the progressive development of the technology.
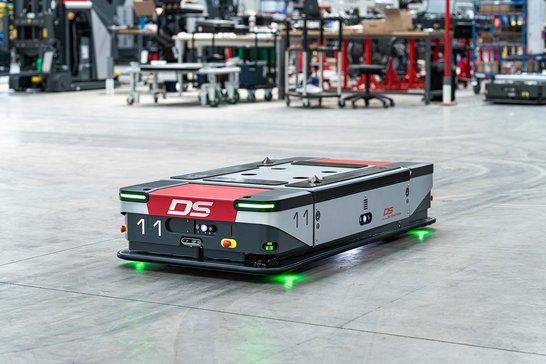
Automated Guided Vehicles (AGVs)
AGVs are traditional driverless transport vehicles that operate along predefined routes. They travel along rigidly predefined routes and bring the respective transport loads to their destinations. Each lane, turn or intersection is carefully planned by the mobile robots to achieve the highest efficiency of the overall system. Mutual obstruction of the vehicles or even blocking is thereby ruled out.
Autonomous Mobile Robots (AMRs)
AMRs are very similar to AGVs, but far more flexible and responsible for achieving their objectives themselves. They are often only provided with the target and a map of the operational environment. Using sensors, the mobile robots then continuously record their surroundings and can react independently to changes. Planning their paths independently allows them to avoid obstacles, but carries the risk that decisions made may negatively affect the efficiency of the overall system. The individual vehicles can interfere with or even block each other.
Quick Response Robots (QR-Bots)
QR bots form a special category of mobile robots because, unlike the other two vehicles, they are not collaborative. Compared to AGVs and AMRs, they have far less sensors and safety devices and are therefore used for simpler and limited tasks.
AGV or AMR
Currently, companies are faced with the decision of choosing between AGVs and AMRs. As the positive features of both mobile robots are appealing to many plant operators, this decision often becomes a challenge. Regarding this, DS Automotion has set a milestone in the industry by combining the strengths of both worlds, AMR and AGV, with the ARCOS vehicle software. The customer has a transport system at his disposal, which optionally uses autonomous functions or follows tracks predefined by the user. This is the first time that the best features from both worlds, maximum flexibility and maximum efficiency, have been realized in a single transport system. In 2023, DS Automotion also won the IFOY Award in the software category for the development of this technology and turned either or into as well as.