In just six months, SSI Schaefer was able to automate the existing mobile racking system at Ostendorf in Emstek using automated guided vehicles (AGV) and its WAMAS® intralogistics software. Right after the go-live in the middle of 2021, the positive impact of this partially automated logistics solution was clear and quantifiable: it ensures transparent, error-free processes and makes the material flow resource-independent – and thus more efficient – in three-shift operations. Achieving these objectives was an important step for this plastics specialist in order to meet its customers’ increasingly specific demands and strengthen its position on a highly competitive market.
Share article
Gebr. Ostendorf Kunststoffe GmbH
is one of the leading manufacturers of wastewater pipe systems in Germany and has sold these plastic pipes and polypropylene fittings since 1973. Its customers come from the construction industry, which generally orders large quantities of a wide range of variants and operates in a cost-intensive environment. Given its ongoing growth and the demand for shorter and shorter delivery times, Ostendorf had already commissioned a new distribution center at its headquarters in Vechta in 2017 for packaging-optimized overnight goods staging. SSI Schaefer equipped the center with an automatic channel storage system including SSI Orbiter® load handling devices, WAMAS® intralogistics software and a conveyor system.
The Path to Semi-Automation
At its Emstek site, Ostendorf also faced the challenge of adapting processes to increasingly demanding market conditions. It needed to optimize intralogistics, increase productivity and cut costs. At the same time, Ostendorf entered into an agreement with a major construction industry customer for pre-picking goods onto mixed pallets. That meant that suddenly, there were more packaging materials and pallets that had to be kept on hand and moved around the warehouse. However, it is not easy to recruit qualified staff for the additional work involved, as well as for three-shift operations – especially in the Oldenburg Münsterland region, which enjoys nearly full employment. Therefore, Ostendorf chose a partially automated plug-and-play solution from SSI Schaefer that could be installed quickly and is ideal specifically for smaller warehouses with moderate throughput rates. The new solution, combining automated guided vehicles (AGV) with the existing mobile racking system (MRS), handles the storage and retrieval processes and internal transport reliably, offering Ostendorf the advantage of high process reliability around the clock.
Ostendorf chose SSI Schaefer because it wanted a single partner that could serve as the general contractor for the whole solution, including all the interfaces. This made communication much easier and ensured a time-optimized project schedule. Furthermore, the two companies already had good experience collaborating on other projects, such as the high bay warehouse in Vechta and the mobile pallet racking system in Rain am Lech, in which SSI Schaefer proved a reliable expert partner. Last but not least, Ostendorf was already familiar with the WAMAS® intralogistics software from the Vechta site and had had good experiences with it.
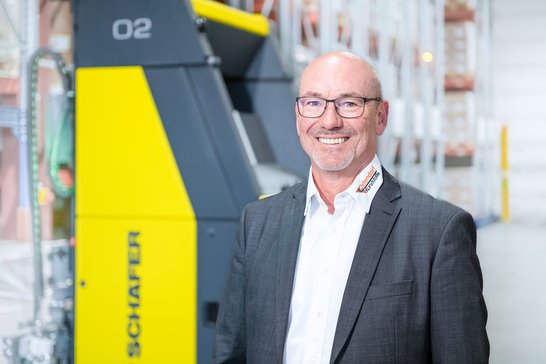
“For Emstek, relying on full automation, as was done at Vechta, would have been wishful thinking and excessive,” reports Ludger Stroot, operations manager for Emstek at Ostendorf. “But we still wanted to introduce a certain degree of automation to get the benefits that come with it. In this context, the automated guided vehicles were the appropriate technology and were just right for our comparatively low throughput.” “In addition, time was tight,” adds Lukas Varelmann, head of in-house logistics at Ostendorf. “While the planning and implementation of a fully automated high bay warehouse, including the building permit, takes at least three years, we were able to achieve our objectives in less than six months thanks to partial automation.”
A Practical Combination of an MRS, AGVs and Software
This extremely manageable timeframe highlights the particular advantages of the scalable logistics solution that was introduced here: “The combination of a mobile racking system with automated guided vehicles is a mature standard and can be directly integrated into the customer’s warehouse structures,” explains Stefan Reichwald, sales manager at SSI Schaefer. “The automated pallet handling solution immediately has positive effects on delivery reliability and quality, as well as ongoing operating costs.”
SSI Schaefer successfully completed this partial automation project together with AGV specialist DS Automotion, an SSI Schaefer Group company, in the middle of 2021. In the process, the partners set up an interface to the existing mobile racking system. At the same time, they were responsible for the integration of the AGVs and conveyor system and for the overall integration into Ostendorf’s WAMAS® software environment. “This was a comprehensive solution package, including software, so the decision to implement it in this form was an easy one,” emphasizes Lukas Varelmann.
Improved Workflow and Continuous Material Flow in 24/7 Operation
“The AGVs ensure a constant material flow in three-shift operation at Ostendorf; the processes are clearly structured, and this approach virtually eliminates defects,” explains Roland Hieslmair, sales engineer at DS Automotion. This reduces the workload of employees, whose current responsibilities include cross-process activities in the control center.
All the processes are also clearly traceable via WAMAS®. Furthermore, the secure, reliable communication between the MRS and AGVs eliminates waiting times; as a vehicle approaches its destination aisle, the system opens the aisle already. The software communicates with the mobile racking system via ProfiNet with barcode support.
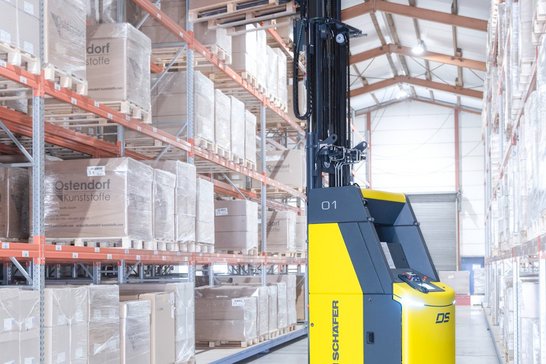
“WAMAS® sends the orders to DS Automotion’s fleet controller, which you can think of as a kind of ‘dispatcher’”, explains Roland Hieslmair. The system simultaneously checks which vehicle is free and issues the transport command. For a retrieval order, WAMAS® makes sure the aisle opens promptly so the AGV can drive right in, pick up the requested pallet and move it to the transfer point on the conveyor system. The fleet controller notifies WAMAS® that the order is complete, and the AGV is now ready for its next task.
Linking DS Automotion’s solutions with SSI Schaefer’s portfolio offers customers the opportunity to reap the benefits of integrated solutions without interface problems; a central contact person is always available, and laborious coordination among different systems is eliminated.
Additional Benefits for Ostendorf
When companies grow and seek to increase the efficiency and quality of their order processing, they – like Ostendorf at its Emstek site – often consider introducing software in conjunction with automated processes. The combined system solution, consisting initially of an MRS and two AGVs, increases efficiency for this plastics specialist by having the AGVs operate continuously, with no breaks. With the vehicles used, SSI Schaefer not only met Ostendorf’s time target for double cycle use, but actually exceeded expectations;
the AGVs complete the double cycles about 30% faster than even required. If even higher performance is required in the future, additional vehicles can be added without difficulty. Modern sensor technology makes the vehicles safer for employees than conventional forklifts. In addition, the AGVs pay for themselves quickly. The same is true of the extremely space-efficient mobile racking systems, which SSI Schaefer offers in combination with AGVs as a solution package from a single source exclusively.
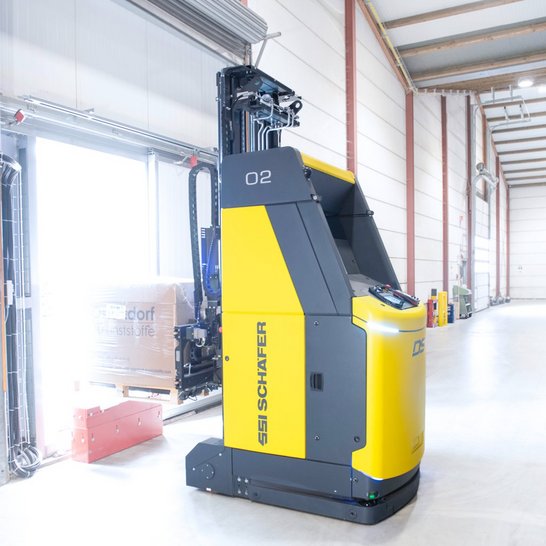
Continuing a Successful Project Partnership
Together with SSI Schaefer, its partner of many years, Ostendorf hopes to repeat the success achieved in Emstek at another location. There as well, the aim is to establish a solid operational foundation to perfectly meet the growing demands of the construction industry – for example, through order-specific pre-picking. Initial scenarios are also being considered for construction of an automated small parts warehouse in Vechta. Ludger Stroot and Lukas Varelmann agree: “The professional project management and fast implementation impressed us once again.” “The two sides worked in harmony, the approach was always solution-oriented, and the cooperation was always positive. The results we achieved were thoroughly positive and speak for themselves.”
In partnership with SSI Schaefer, Ostendorf has implemented an impressive partially automated warehouse solution. They automated the existing mobile pallet racking by combining it with the new AGVs and connected both components to the new WAMAS® software. This solution gives Ostendorf an efficient, optimized storage, transport and picking process and strengthens its competitive edge.