The initial situation in Arburg's transport logistics was clear: the extended assembly areas created by a new hall made it necessary to expand the internal conveyor systems. The new, third assembly hall, which was built in 2019/2020 as an extension of the two existing halls, had to be connected logistically. The existing assembly halls are supplied from the central high-rack warehouse using an electric monorail system. The new transport system was designed to be driverless from the outset and integrates the new hall into the existing logistics chain, ensuring a continuous, smooth supply to all three halls.
Share article
Why was an automated guided vehicle system (AGV) chosen?
Helmut Stumpp, Group Manager Transport, answers the question as follows: "First of all, the AGV offers much greater flexibility at pick-up and drop-off points than the existing automatic systems, such as the electric monorail system. Deliveries can be made directly to the worker and collections can be made directly at the 'workbench'. The entire system can be used in three shifts and can be expanded more quickly, cheaply and easily with additional transfers. This has enabled us to further increase our level of automation in assembly and we have managed without interfering with the building fabric of the halls, which was also very important."
The objective
It's easy to read: the AGV is to transport Arburg pallets with special dimensions, half-Euro and Euro pallets as well as machine bodies over a total travel distance of around 350 meters to the latest assembly hall. A total of seven automated guided vehicles (AGVs) with seven battery charging stations are used for this purpose - one for each vehicle. The terminals operate web-based on the basis of the existing Wi-Fi radio network at Arburg.
Six of the seven AGVs are automated forklift trucks of the "AMADEUS" type, which are used to transport pallets. The Arburg pallets with frames measure 1,400 x 1,000 x 350 millimetres and can carry a maximum weight of 1,750 kilograms. The Euro pallets with frame measure 1,200 x 800 x 330 millimeters and can be loaded with 1,000 kilograms. The size of the half-Euro pallets with frame is 600 x 800 x 300 millimetres and the load capacity is 750 kilograms.
There is also another AGV for machine stands with impressive dimensions of 5,000 x 1,700 x 2,250 millimetres, which in turn allows a payload of 1,800 kilograms. Among other things, the so-called "4-way AGV" can move forwards in "crab steering". This diagonal steering allows a vehicle to be moved crosswise so that the path of travel can be kept as narrow as possible. The vehicle is equipped with a plate conveyor and a data light barrier. An occupancy sensor is also fitted to check whether there is a load carrier on the slat conveyor.
With all AGVs, the goods to be transported do not protrude beyond the dimensions of the pallets or vehicles. It is also important to note that the automated guided vehicle system is only used indoors during assembly and is therefore not exposed to the weather.
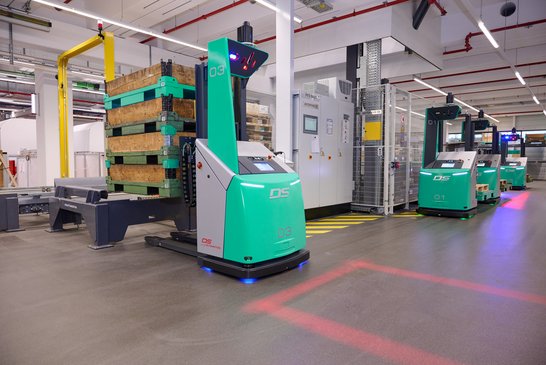
Challenges in the project
An important aspect with a significant impact is the other "road users" on the planned AGV routes. At Arburg, this involves "normal" passenger traffic as well as tugger trains, bicycle traffic and various industrial trucks such as forklift trucks, low and high lift trucks. In order to be able to transport autonomously, the AGVs must therefore recognize obstacles and stop in front of them. To prevent damage, the flat forks of other industrial trucks in particular must be detected.
Prepared for everything
The navigation of the AGVs works with lasers in combination with environmental features. This achieves a positioning accuracy of +/- 20 millimeters. The vehicles drive to "their" charging station independently and in good time to recharge themselves.
For future expansion, routes of encapsulated layouts are also possible. The number of vehicles can be changed at any time during operation. This allows the company to react flexibly to future growth.
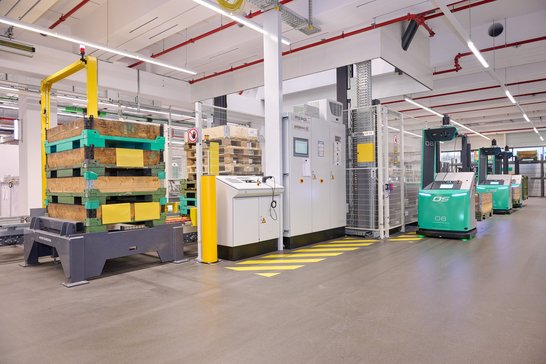
Transport and transfer points
The electric monorail system (EMS) and other industrial trucks transport all parts and components required for assembly from the high-rack warehouse to the three assembly halls. The AGV extension was planned and implemented in the passageway between the two existing assembly halls and the newest assembly hall, which, according to Helmut Stumpp, started transport in May 2023.
From June to August, the material flow was completed by a pallet lifter to the first floor of the new assembly hall. The transport volume of the extension is around 30 transports per hour, excluding machine body transports. These are only required to a lesser extent.
Example: Removal process from the machine column storage area
A total of 14 steps are required to remove a machine upright from the warehouse using the "4-way AGV" - a good example of the complexity of the processes required to operate an automated guided vehicle system smoothly.
First, the transport order for retrieval is created in the transport control system. The AGV then drives to the machine rack warehouse and registers in front of the access gate. The transport control system sets the retrieval order to "active" status if no other order is pending. The storage crane moves to the storage location (source), picks up the machine stand and clears the entry area for the AGV. The transport control system then gives the AGV the travel order to drive from its intermediate position into the machine column storage area.
The warehouse signals entry clearance (gate clearance) to the AGV, the AGV drives in and signals "Position in warehouse reached" (release warehouse and "Close gate"). The "4-way AGV" is loaded, the warehouse reports the loading and the approach to the alternative location. The AGV now registers the exit, whereupon the warehouse issues the exit release. After the exit has taken place, the AGV reports in front of the gate again. The machine column storage system closes the gate and activates the storage crane again for new orders on the electric monorail system. Then comes the final step: the AGV moves the machine column to the lifter in the assembly hall and reports its arrival.
How the transport goods are handed over
The sources, i.e. the transfer points from the monorail overhead conveyor to the automated guided vehicle system, are divided into pallet delivery and machine body/machine column pick-up. The pallets are transferred from the overhead monorail to a chain conveyor, from which the AGV picks up the pallets on the opposite side. This avoids crossing traffic between the two transport systems.
The "4-way AGV" independently retrieves the machine bodies from the warehouse. The AGV and monorail overhead conveyor cross here. The lowering points of the AGV, which are the delivery points in the latest assembly hall, are located in the basement. Here, too, the delivery is split into two parts, again via a chain conveyor for the pallets.
The machine uprights are transferred via a second floor lifter with an attached slat conveyor and lifted to the first floor. On the first floor, both pallets and machine bodies are then transferred to the corresponding conveyor system.
System integration of the AGV
With the changeover to SAP EWM for the efficient management of warehouses and the processing and monitoring of goods movements in 2022, transport orders will be sent from SAP EWM to the transport control system via interfaces. From there, they are then distributed to the subordinate systems or interface systems. The AGV is connected to the transport control system. Communication in the interface is controlled via telegrams consisting of header and user data.
The press release was written by Arburg.
This and other press releases can also be downloaded from their website at www.arburg.com.