Service
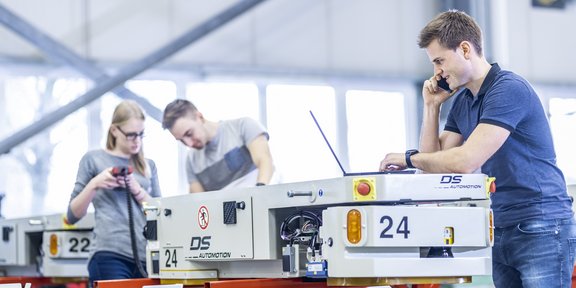
Our services
Every maintenance is an optimization. Our experienced team carries out predictive maintenance worldwide. With a precise analysis, we record the actual condition, identify deficiencies and draw attention to possible future weak points. These are eliminated by the comprehensive competence of our system technicians in a time- and cost-saving manner and the system is optimized. Maintenance and repair services carried out by DS Automotion avoid downtimes and guarantee you a high availability of the plant.
Available spare parts are a guarantee for assured plant availability. Especially in times of uncertain material availability and the resulting delivery problems, this topic is becoming increasingly important. Standard spare parts are usually at the customer's site within 24 hours, customer-specific components are delivered adapted and are plug-and-play. We are a partner for spare parts packages, consignment stocks, single spare parts and also well positioned for component repair. Repairs can be carried out for the most part at short notice and at low cost in our in-house laboratory. We guarantee that you will receive the desired spare part or a suitable alternative solution reliably and quickly, even after years.
Data garbage accumulating over time can limit the performance of your AGV system. During software maintenance, we perform analyses in this regard, clean up storage media and databases, and install updates if necessary. This ensures the stability and performance of your transport system. Regular software maintenance also ensures maximum security and up-to-dateness. The networking of your system with DS Automotion enables immediate function checks and analyses of the running operation. Any defects and malfunctions that occur can thus be remedied promptly.
Prepared for the worst case scenario through cluster solutions and personnel training. The master computer is the heart and brain of the plant.
We check the route area of the AGVs for sufficient illumination (SNR). Missing illuminations, roaming problems, failed access points can thus be detected.
Safety and cost savings all along the line through regular checks and performance optimization. Another service offered by DS Automotion includes regular condition checks of the batteries by our specialist. This increases the service life and protects against unpleasant surprises. Weak cells are detected and equalizing charges are carried out. Your advantage: safety in operation, with certainty long service life and with certainty: cost savings.
To ensure that you are never in a legal bind, we offer periodic, timely inspections and liability-relieving documentation. UVV inspections offer reliable protection against liability claims in the event of accidents involving personal injury. Legislation prescribes the annual inspection of components that ensure personal safety. Overlooking inspection deadlines and legal requirements can lead to liability problems. DS Automotion takes over these tasks and carries out the annual UVV safety inspection on schedule.
We ensure efficiency - now and in the future. The only constant is change. Regardless of the services we provide, we are your partner when it comes to process changes in your company. Quickly and reliably, we again ensure optimum efficiency for your plant, even under the new conditions.
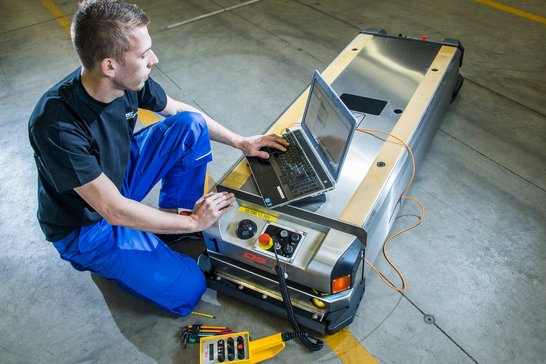
We help quickly and reliably
With our individual standby contracts and our hotline, we offer help for every problem.
We are there for you around the clock and guarantee feedback from one of our system technicians within the shortest possible time in the event of a malfunction. With immediate expert assistance, many malfunctions can be clarified immediately and, if necessary, remedied immediately via remote maintenance. In case of need, the DS Automotion network organizes fast and competent help on site. Because nobody knows your plant better and can help faster.
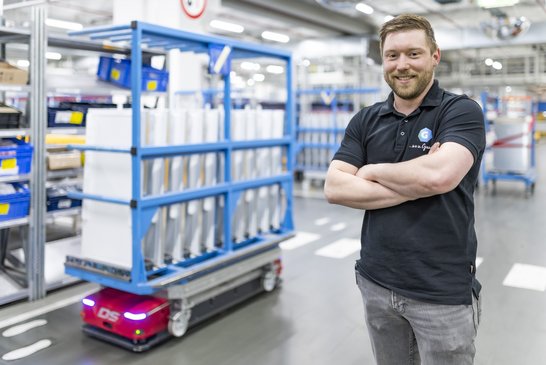
Your employees become plant experts
We train your maintenance and operating personnel to become experts. New employees are introduced to the subject matter and the existing team can perfect their knowledge on the basis of the wealth of experience gained. If desired, individual in-house training sessions can be held to address specific concerns on site.