Stiebel Eltron uses DS Automotion AGV for flexible Heat Pump Assembly
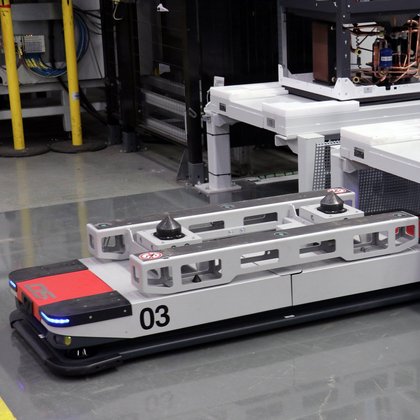
Heat pumps help us reach our climate targets. Instead of fossil fuels, the environment-friendly heating and cooling systems utilize energy from the ambient air, soil or phreatic water. In Holzminden, Germany, Stiebel Eltron manufactures various types of heat pumps on a common, highly flexible production line. There, a driver-less transport system made by DS Automotion takes care of the fully automated transport of the unfin-ished heat pumps between manual work stations that are linked using conventional conveyor systems.
Share article
As well as industry and traffic, building equipment and appliances are turning their backs on oil and gas. Heating, ventilation, air conditioning and refrigeration (HVACR) rely on smart, environment-friendly technology to facilitate the energy transition. Rather than fossil fuels such as coal, oil or natural gas, heat pumps draw energy from the ambient air, soil or phreatic water, using electricity as their operating power.
The electric power heat pumps require is only a fraction of what they supply in the form of heating or cooling energy. These future-oriented systems substantially reduce carbon emissions induced by heating and cooling. This technology is a key to achieving climate targets.
Flexible Heat Pump Production
Stiebel Eltron GmbH & Co. KG is a globally leading heat pump manufacturer based in Holzminden, Germany. Established in 1924, the manufacturer of electrical implements, room heaters and water heaters is among the pioneers of this technology, commencing heat pump development and production during the oil crisis in the nineteen-seventies. Since then, the general increase in consciousness for the environment and the climate change fueled a rising demand. Long before the recent geopolitical distortions accelerated this trend with a steep increase of gas prices, Stiebel Eltron decided to expand its production capacity at its Holzminden factory,
The 2,000 employees in the heat pump competence center there produce numerous air source, ground source or water source models in various performance categories for outdoor and indoor use. This wide product variety and demand fluctuations took the model-specific assembly line to their limits, where the unfinished heat pumps were moved between work stations on pushcarts. This concept proved less than flexible.
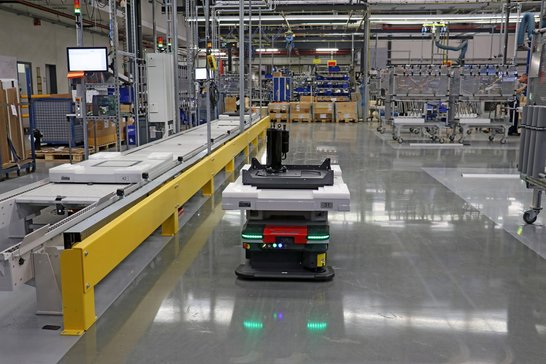
The “Streamlining and Equipment” department consequently designed a highly flexible production line for air-to-water heat pumps they termed “Multilinie”. It was meant to be capable of producing all types including all variations in low quantities down to lot size one. “The assembly sequences of the various models differ greatly, preventing a rigid continuous assembly line”, explains Roman Flegel, M. Sc., Stiebel Eltron streamlining process engineer and Multiline project manager.
Mixed System with AGVs
As all manual tasks until compressor placement can be performed in equal work cycles, the first two manual workstations within Multiline are linked with a pusher chain conveyor. The work cycles of the subsequent step where the refrigerant circuits are soldered are considerably longer and vary from model to model. This is why a driverless transport system with automated guided vehicles (AGV) takes care of the transport to these four stations.
The same applies to the subsequent transport to where the evaporators are added, to the test chamber and finally to a buffer storage. From there, AGVs haul the heat pumps to a transfer point, where a conveyor system takes over and transports them to the manual work stations where cabling, insulation and housing are added.
Successful Partnership
The Stiebel Eltron streamliners already had years of experience with driverless transport systems, so they did not have difficulties adopting this technology for their concept. The “Streamlining and Equipment” department also acted as the prime contractor in the implementation of the Multiline installation with its variety of technologies.
For the rigid conveyor systems, Stiebel Eltron awarded the contract to Knoll Maschinenbau GmbH. This company also supplied the carrying fixtures that can be adapted using plastic receptacle inlays made by Stiebel Eltron to support all sizes of heat pumps. These fixtures are used on the rigid conveyors as well as the AGVs.
Due to limitations of the maneuvering area, the AGVs need the ability to moves completely surface-mobile through the course to serve the buffer storage. The contract went to DS AUTOMOTION GmbH. The experienced Austrian AGV system manufacturers have been solely developing and producing driverless transport systems for nearly 40 years. Their systems enjoy a favorable reputation for their reliability and suitability for industrial applications. “DS AUTOMOTION was the only manufacturer able to offer a suitable omnidirectional undercarriage AGV”, says Roman Flegel. “Also, their NAVIOS fleet manager software not only allocates transports to vehicles but also takes care of the administration of the buffer storage.”
Omnidirectional Transport
The OSCAR undercarriage AGV can navigate in confined spaces. Due to the servo motors of its proven drive technology, it boasts smooth running and high positioning accuracy even in particularly narrow stations. The vehicles maintain their course with free navigation using contour-based (SLAM) localization. At the Stiebel Eltron plant, this is supplemented by dead reckoning using magnets embedded in the ground at regular intervals to further improve precision. Thanks to their extremely low build with only 310 mm shoulder height, the AGV is suitable for a wide variety of undercarriage transport tasks.
“Within the Stiebel Eltron Multiline, OSCAR omni not only carry the heat pumps on the carrying fixtures between the manual work stations”, states Kai Hoffmann, Sales Manager Germany with DS AUTOMOTION. “They also supply the soldering stations with the required material in trolleys.” With an integrated 160 mm lift, they can automatically pick up and set down loads up to 1,000 kg. “Driverless transport using OSCAR omni allowed us to reduce the area required for the buffer storage by 50 percent”, Roman Flegel stresses. “This also keeps distances and trip times short so we only need four vehicles.”
Fleet Management and Beyond
The NAVIOS fleet manager software calculates the driving tasks for the AGVs, using data it receives from the ERP system as well as the conveyor system. With this, it communicates using the open UPC UA protocol, among other things to coordinate the load transfer. NAVIOS also administers the buffer storage. Its functionalities range far beyond those of fleet management itself.
Not only at the Stiebel Eltron plant but in all recent and future installations, NAVIOS uses the standardized VDA 5050 interface to communicate with AGVs. “This provides users with the freedom to use third-party vehicles as well, if these are better suited for the specific transport task at hand”, Kai Hoffmann explains, and Roman Flegel adds: “Even though we currently do not see no reason for this, it is comforting to know we have the option in case of need.”
Industry 4.0 Showcase
Although due to the high order level, production had to continue in parallel, Multiline was built and commenced production in less than a year. “The line has been working in a three-shift operation since it was commissioned in mid-2021. In addition to faster reactions, it also gives us the opportunity to produce new product types or pilot series there”, says Roman Flegel. “Linking product and order information with the intelligent, AGV-based transport solution, with our partners, particularly with DS AUTOMOTION, we jointly created a digitalization and Industry 4.0 showcase.”
As it frequently happens in projects based on the latest technologies with this complexity and numerous interfaces, the start was not frictionless. “DS AUTOMOTION did not let us alone with this and were always immediately at hand for problem-solving or modifications”, Roman Flegel confirms. “After some ‘teething troubles’ were treated, Multiline has been brilliantly fulfilling all our expectations, ensuring long-term efficient and economic heat pump production.” Most importantly, it facilitated the envisaged increase in production capacity, allowing Stiebel Eltron to double the output on the same floor space.
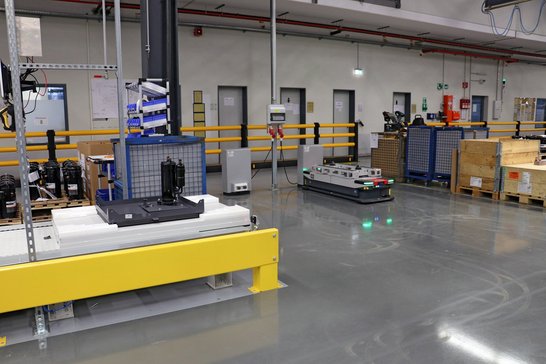
Further Expansion planned
Appetite comes with eating. Heat pump production automation will in a next step be extended to include the above-mentioned final assembly, including final cabling and insulating. There are also plans to integrate final testing and packaging with the automation solution.