The best of both worlds
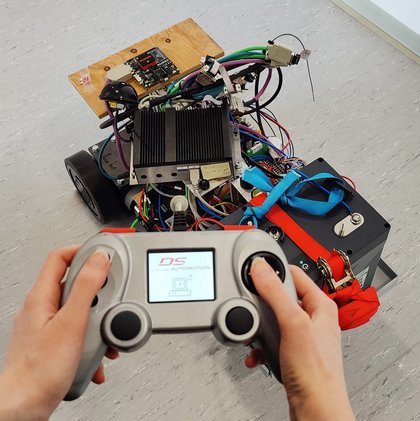
The characteristics of reliable and efficient are no longer a contradiction. DS Automotion has succeeded in combining the advantages of AGV and AMR as part of a joint research project with RISC Software GmbH and MTA GmbH. The motto is "plannable autonomy" and the project is called MicroAGV. The new navigation technology enables the vehicles to navigate completely autonomously as well as to drive "virtually" lane-guided if desired. DS Automotion thus solves an important problem for users to improve system performance.
Share article
Reliability and efficiency
These helpers are on duty around the clock, they know no hunger and no fatigue. They simply work. We are talking about automated guided vehicles (AGVs) or autonomous mobile robots (AMR). They take over precise delivery tasks in the production process, relieve human colleagues and ensure precise processes. They are mainly found in highly automated productions. However, many users are concerned with a particular problem: traditional AGVs have to follow a predefined track and thus cannot react to changing environmental conditions - AMRs score with a higher degree of autonomy in selecting travel paths and dealing with obstacles, but they have the disadvantage that the higher degree of freedom reduces the efficiency of the facility. Developers at DS Automotion, a world leader in AGV/AMR, have now found a way to combine the best of both worlds and, under the project name "MicroAGV," have further developed navigation technology in line with the motto "plannable autonomy." "Together with our research partners RISC Software GmbH and MTA GmbH, we have combined the flexibility of AMR on the one hand and the reliability as well as efficiency of classic AGV systems on the other hand," explains Andreas Richtsfeld, Division Manager Technology and Product Development at DS Automotion.
In the process of the research project, the vehicle's hardware architecture was also slimmed down so that smaller and more cost-effective AMRs can be offered in the future. "At the moment, the MicroAGV is in the development phase. However, together with our project partners RISC Software GmbH and MTA GmbH, we have built an initial functional prototype," says Richtsfeld.
Kurt Ammerstorfer, Division Manager Sales, Product Management and Marketing at DS Automotion ventures a glimpse into the near economic future of the company: "We hope that the new navigation technology will give us a competitive advantage that will also be used in future products and projects." The new method has already been implemented in the Sally Courier, which transports sterile goods, documents, laboratory samples, instruments and medicines, among other things, in medical facilities.
Fully autonomous and lane-guided in one system
AGVs operate in a "virtual" lane-guided manner to ensure constant performance in supplying and removing the required parts from the production lines. They navigate along virtual guidance lanes - but without the ability to leave the predefined lanes. Those who want things to be a bit more autonomous rely on AMRs. They can perform certain functions autonomously and make decisions on their own. This makes their use very flexible, as the working environment needs to be less regimented and less structured. Navigation is usually based on contour-based technology
The MicroAGV can navigate completely autonomously, but can also drive virtually track-guided like an AGV if desired. For this purpose, the research project implemented the recording of the environment by means of 2D (laser scanner) and 3D sensors (ToF cameras). Also integrated: reactive navigation, in which the paths of other vehicles are also taken into account in the vehicle's own path planning. For this purpose, the planned driving trajectories of other vehicles are integrated into the own planning. The newly developed navigation algorithm has already shown good results in the first simulations.
Thanks to communication with other vehicles or operating equipment, the MicroAGV can adjust its path planning accordingly and prevent blockages. "It is also possible for the user to manually plan at which points the behavior of the vehicles must act either like an autonomous mobile robot (AMR) or like a (virtual) lane-guided AGV. The customer can decide whether to allow flexibility in certain areas with regard to autonomous navigation, e.g., to avoid obstacles, or whether he needs strict rules and the associated efficiency to ensure his process times," Richtsfeld elaborates. In concrete terms, this means that zones can be defined that force the vehicle into a predefined lane, for example at bottlenecks or intersections to avoid collisions.
New drive
A compact and gearless direct drive was developed for the MicroAGV. In the laboratory and on the functional prototype, the maximum torques and jerk-free operation at a speed of 1 rpm were demonstrated in various tests. Using a specially developed dual-axis controller, the two drives are controlled via a CAN bus system. To ensure that the STO (Safe Torque Off) safety function meets all legal framework conditions and standards, this function had to be tested and certified by an accredited authority. "In our case, this is TÜV-Nord, which has been part of the team since the start of development and carried out the final fault installation tests," reports Richtsfeld. The certificate was already issued in December 2021.
With the successful implementation of the research project, DS Automotion has succeeded in creating the basis for numerous AMR applications. For this purpose, a construction kit of electrical, electro-mechanical and software components is now available, with which different products for the most diverse applications can be created in the future. But the cooperation of the consortium has also worked very well, according to those involved in the project. "It is already certain that the collaboration will continue after the research project is over," Richtsfeld reveals. This is not only to extend the scope of the current project, but also to new projects and research fields that have emerged during the period of cooperation.